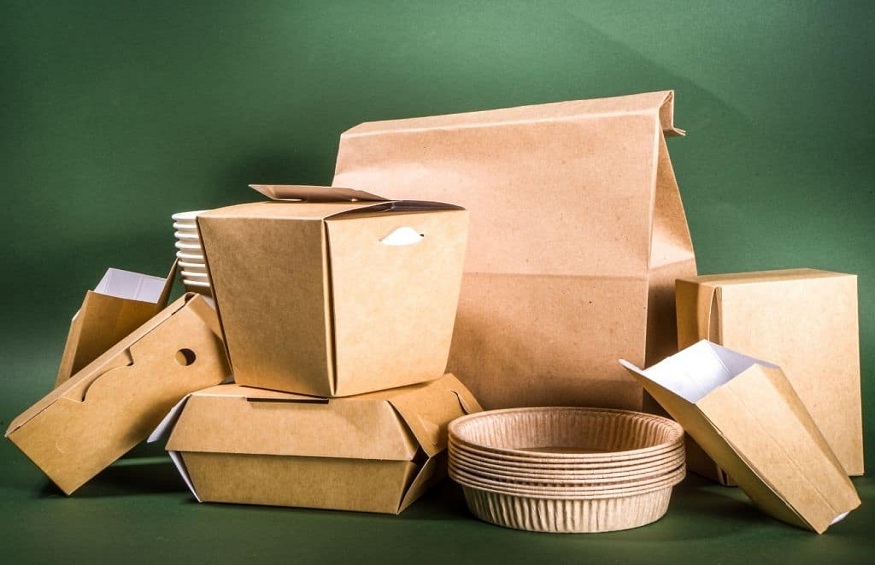
How Do You Select the Best Providers of Flexible Packaging Materials for Your Food Packaging Items?
Food packaging companies must select the best flexible packaging material supplier. Products are protected, shelf life is increased, and a positive customer image is formed in large part by the packaging. That being said, it might be overwhelming to choose the right supplier because there are so many flexible packaging alternatives available. The following advice might help you choose providers who can fulfill your needs and navigate the flexible packaging division.
Prerequisites for packing:
Ensure you first specify what you need to be packaged. Think about things like the sort of food being packaged, budget, desired distribution methods, shelf life targets, and sustainability priorities. Paper, foil, plastic films, and other materials are examples of flexible packaging. Considering the unique needs of your product, decide which material attributes you’ll need. The ability to withstand moisture, for instance, is crucial for snacks but might not be as significant for dry items.
Elastic materials for packaging:
Find more about the benefits and drawbacks of the many flexible packaging materials that are offered. Each is suitable for varied applications due to its unique strength, barrier, and printability qualities. Take the sustainability profiles of the materials into consideration as well; certain materials are more recyclable after consumption than others. Recognizing vendors with the best possibilities requires an understanding of material science.
Examine possible suppliers’ portfolios to determine whether they provide the kinds of food packaging products and formats you require. Choose vendors who can manage the quantity, minimums, and production schedules of your order and have experience packing food. One-stop shopping is convenient when suppliers have their own printing, laminating, and conversion facilities. To save money and reduce lead times, think about using suppliers who are close to your packaging or product distribution areas.
Obtain samples:
Get samples from the vendors on your shortlist so you can evaluate the suggested materials and packaging ideas. Look for flaws in the general quality, strength, and barrier characteristics. Ask vendors to submit technical data sheets that detail the composition of the materials and the outcomes of performance tests. To verify the dependability of the supplier, the quality of the customer service, and the cost structure, ask for references from comparable customers. For a price comparison, request a quote.
Follow up on order needs, deadlines, art files, and other production details with your suppliers once you’ve made your selections. For early problem detection, request pre-production proofs or samples. Evaluate conducting facility audits of suppliers to ensure that food safety and quality requirements are being fulfilled. Where relevant, ask for certifications. Don’t forget to pay invoices on time and give constructive criticism to maintain good relations.
Open communication:
Open communication is crucial during the packaging creation and production process, once a supplier has been chosen. Indicate all order requirements in detail, such as deadlines, minimum order quantities, material needs, and artwork files. To identify problems before they become serious, ask for test runs, samples, or pre-production proofs. In the long run, being proactive helps to prevent expensive errors or delays.
Assistance with technology:
Furthermore, vendors must be prepared to offer technical assistance as required. Proper storage, the outcomes of shelf life tests, recycling guidelines, and regulatory compliance are some of the topics that may come up. To maximize the performance of packaging, rely on the material science knowledge of suppliers. To make sure that quality and production requirements are upheld, periodically audit the facilities of suppliers and request certifications related to food safety, if necessary.
Food businesses and merchants are finding that sustainability is a crucial aspect. Assess the priorities and profiles of suppliers about sustainability. Seek those that minimize waste during production, seek recyclability certificates, and use recycled content. Every year, partners should submit measurements and be open about their sustainability goals. Ask for third-party certifications.
Reexamine supplier connections regularly as your business and packaging demands change. A changeover could be prompted by updates to rules, new materials, or sustainability goals. It’s easier to find fresh possibilities if you keep up with industry trends. Encourage ongoing growth in your relationships by giving feedback. When it’s feasible, give higher order volumes to vendors who perform well.
Reduction of risks:
To reduce risk, think about using two sources. This guards against shortages or delays in manufacturing if one supplier experiences problems. Retain a capable backup supply on hand in case something goes wrong. To guarantee competitive pricing as the market shifts, periodically issue requests for proposals . Assess suppliers’ performance and expenses by comparing them to rivals in the flexible packaging market to hold them responsible.
Choosing flexible packaging suppliers should consider a few additional elements in addition to the previously outlined basic criteria. Lead times and shipping costs might be impacted by geographic proximity. Local vendors could provide quicker turnaround times and reduce shipping-related pollution.
Having enough production capacity and warehousing space to accommodate demand surges is another crucial factor for suppliers. The worst situation is when a supplier’s capacity prevents them from completing massive requests. Think about different sizes of providers as well; smaller businesses can provide more individualized service, but larger ones might have greater resources.
Finally, keep up a good rapport with suppliers by offering suggestions for ongoing development. Increased order volumes should be given to high-performing partners whenever it is practical. To promptly resolve any problems that may occur, keep the lines of communication open and collaborate. The strongest, most long-lasting supplier relationships are those that are built on mutual trust and cooperation.
Food firms can establish durable partnerships with flexible packaging suppliers through consistent communication, implementation of quality assurance procedures, and regular evaluation. To continually supply compliant, high-quality products and achieve sustainability targets for many years to come, choosing the right partners is essential. Over time, needs change, and suppliers can offer insightful information and solutions by keeping lines of communication open.
Conclusion:
Consider the supplier selection process again from time to time when your packaging needs to change. A transition could be prompted by legal modifications, material advancements, or sustainability objectives. It’s important to stay up with market developments to find new opportunities and maintain the credibility of existing vendors. Food businesses may get solutions that safeguard goods and brand reputation for many years by conducting thorough research on flexible packaging material suppliers.